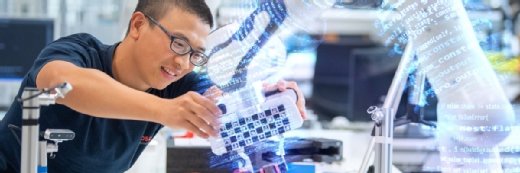
IIOT : des gains à la hauteur des défis
L’appétence des industriels pour équiper leurs usines en objets connectés et connecter leurs machines est là. Mais l’acquisition des données n’est pas le seul défi à relever pour optimiser ou automatiser véritablement ses processus de production.
Différentes études menées sur l’IIOT ces dernières années montrent les attentes fortes et l’appétence des industriels pour équiper leurs usines en objets connectés et connecter leurs machines. L’acquisition des données n’est malheureusement pas le seul défi à relever pour optimiser ou automatiser véritablement ses processus de production. La mise en place de technologies capables de transmettre, traiter et communiquer les données collectées est impérative, afin de constituer un écosystème cohérent et performant. Il faut notamment :
- Un système de télécommunications performant capable de transmettre des données en temps réel,
- Des passerelles (middlewares) capables d’interfacer les systèmes qui produisent et collectent des données,
- Des plateformes de stockage et de sauvegarde des données,
- Un système d’information robuste enrichie d’une couche d’information cognitive permettant un nettoyage, un croisement et une corrélation pour transformer les données,
- Un logiciel de data visualisation permettant la restitution des informations,
- Un dispositif de sécurité global du SI.
Les entreprises industrielles, peu habituées à la maîtrise de la continuité numérique de l’information, subissent les temps longs des implémentations IoT au sein des usines. Cela met à rude épreuve la patience des dirigeants et opérationnels, qui attendent tous un ROI important qu’il soit d’ordre économique, écologique ou encore le bien-être des collaborateurs.
Le défi environnemental
1,2 Milliard d’euros. C’est le budget mobilisé par le gouvernement dans le cadre du plan « France Relance » pour accompagner l’industrie dans sa décarbonation. L’IIOT est un des vecteurs sur lesquels s’appuient les industriels pour mesurer leur impact sur la planète.
L’IIOT permettra aux industriels – et ce pour tous les secteurs d’activités (agroalimentaire, automobile, pharmaceutique…) – de mieux analyser et mesurer les conséquences de leurs activités sur l’environnement en récupérant, stockant et en analysant la grande quantité de données collectées grâce à ces dispositifs.
Avec à ces outils, les industriels auront notamment la possibilité de :
- Diminuer les émissions de gaz à effet de serre liés aux transports. C’est ainsi que Suez a pu diminuer de 7 % les émissions de 13 déchèteries, suite à l’équipement de boîtiers connectés sur 210 bennes qui ont permis d’optimiser la collecte des déchets.
- Diminuer et rationaliser la consommation d’énergie en intégrant des capteurs d’énergie, de température ou encore d’humidité dans les usines afin de mieux comprendre les sources de consommation d’énergie et de prendre connaissance d’axes d’améliorations. En intégrant des capteurs dans un de ses laboratoires, Schneider Electric a déjà pu économiser près de 20 % de sa consommation d’énergie en semaine et près de 38 % le week-end.
Les cas d’usages de l’IIOT pour répondre à ces défis sont nombreux et cette technologie permettra aux industriels de contribuer à la lutte contre le réchauffement climatique.
Une qualité de vie au travail améliorée
L’industrie 4.0 s’intéresse à remettre le technicien au cœur du processus de décision. En plus de décharger les opérateurs des tâches rébarbatives, grâce à l’analyse des données et l’automatisation des processus (réglages machines suite à l’analyse des défauts par exemple) qui participent à l’amélioration de la qualité de vie au travail des techniciens, les dispositifs IIOT améliorent leur sécurité au sein des usines.
Les données récoltées et analysées en temps réel permettent de définir des cas d’usages pour renforcer la sécurité des collaborateurs œuvrant au sein d’une usine :
- Anticiper les risques d’accident grâce à des capteurs équipés sur le salarié ou encore des DATI (Dispositif d’Alarme du Travailleur Isolé). Les systèmes, interconnectés, permettent d’alerter et de signaler de manière automatique ou volontaire en cas de situations inhabituelles (chute, immobilisation, etc.).
- Sécurité des techniciens à l’aide d’équipements connectés. Par exemple, Ansell (leader mondial des solutions de sécurité) et ProGlove (fournisseur majeur de vêtements intelligents pour l’industrie) annoncent un partenariat afin de développer des solutions pour protéger les mains des salariés sur les sites industriels. À l’aide de l’IIOT et des données récupérées, cette solution permettra de proposer aux travailleurs le meilleur équipement en fonction de la tâche à effectuer, pour leur garantir une sécurité totale.
- Prévenir des risques liés à la santé des collaborateurs. L’IIOT est devenu un allié de taille de la reprise, grâce aux capteurs mesurant la qualité de l’air. Ces capteurs, présents dans les usines, permettent d’enclencher des actions (telles que la ventilation, ou la déshumidification) lorsque la qualité de l’air n’est pas aux standards. Cette innovation va permettre aux employés d’améliorer leur niveau de concentration et de prise de décision, ce qui peut avoir des effets positifs sur leur qualité de vie dans leur lieu de travail et diminuer les risques d’accident.
- Réduire le stress des opérateurs. D’un point de vue opérationnel, la maintenance prédictive permise par l’IIOT permet aux salariés des usines d’effectuer des actions de maintenance anticipée et non suite à la détection d’une anomalie sur une machine. Ce type de maintenance permet aux salariés d’effectuer leurs tâches, sans la pression engendrée par une panne subite d’un appareil qui peut générer de forts coûts pour l’entreprise.
Des gains économiques et des temps d’arrêt moindres
Enfin, chaque entreprise ambitionne de réduire ses coûts pour accroître sa compétitivité. L’IIOT a le vent en poupe, comme en témoignent les nombreuses commandes d’objets connectés de grands groupes ; à l’instar de la SNCF qui a commandé 12 500 capteurs IoT visant à équiper les trains TER, Intercités, TGV et Fret, afin d’améliorer la qualité du service rendu aux usagers, la disponibilité du matériel roulant et générer d’importants gains de productivité. De même, voyant l’opportunité, les acteurs historiques de l’IT et de l’OT comme Siemens, Dassault Systèmes, IBM, Schneider Electric, investissent rapidement dans des plateformes robustes pour exploiter les données issues des capteurs déployés dans les usines et sur le terrain.
Le retour sur investissement de la mise en place de tout l’écosystème IIOT (capter et transmettre les données, middleware, stockage des données, transformation des données, restitution et lecture des données) peut être compliqué à estimer. Néanmoins, certains retours d’expérience font état de gains significatifs concernant les réglages, la maintenance, la diminution des arrêts intempestifs, ainsi que l’accélération des redémarrages des machines qui améliore considérablement le taux de rendement synthétique (TRS). C’est notamment le cas de L’Oréal et Saint-Gobain qui témoignent du succès et du gain de temps qu’ils ont pu observer, en adoptant la solution IOT proposée par la start-up Zozio.
Conclusion
Les industriels ont bien compris l’intérêt d’assurer la continuité numérique au sein de leurs usines et de leurs entreprises. À la base de l’écosystème IOT, les capteurs connectés récupèrent les données issues des machines afin d’alimenter un éventail large d’outils SI : ERP, MES, BIM, Jumeau Numérique, etc. afin d’automatiser le plus largement le plan de production ou de simuler les différents scénarii d’optimisation imaginés.