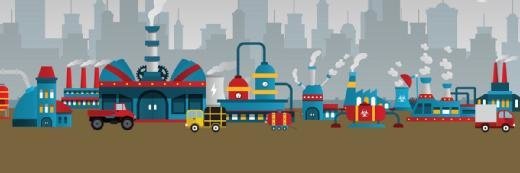
jirikaderabek - Fotolia
Supply chain : comment la planification des ressources de production aide à réduire les stocks
La plupart des entreprises vise à une diminution des stocks (et des pénuries) lorsqu'elles mettent en œuvre un système de planification des ressources de production (MRP). Cela est possible et constitue l’une des marques d’une implémentation MRP réussie. A condition de respecter quelques règles.
Le système de planification des ressources de production (MRP) est le moteur de calcul au sein de l'ERP qui utilise certaines données, comme la demande de produits, les nomenclatures et les informations sur les stocks, pour recommander les commandes de réapprovisionnement (achat et production) nécessaires pour éliminer les pénuries.
Le MRP se concentre sur l'optimisation des stocks, c'est-à-dire sur la bonne quantité d'inventaire pour effectuer le travail. La quantité planifiée de stock est supérieure à zéro en raison de considérations économiques et de quantités supplémentaires qui doivent être planifiées pour réduire le risque de ruptures de stock - causées par exemple par des changements de calendrier, des livraisons tardives, du rebut inattendu, des erreurs de données et autres. Les entreprises doivent inclure des facteurs de compensation dans la mise en place du MRP pour tenir compte de cette variabilité et réduire les pénuries qui, autrement seraient inévitables.
L'inventaire supplémentaire, planifié par le système, s’ajoute aux stocks supplémentaires qui existaient avant le système MRP. Cela se traduit par une augmentation globale de l'inventaire qui compromet les avantages du système. Par conséquent, les entreprises doivent prendre des mesures supplémentaires pour reprendre le contrôle de ces stocks.
Les facteurs de compensation dans le MRP
La solution simple pour réduire les stocks dans le MRP est de réduire les facteurs de compensation: stock de sécurité, capacité de rendement et de rebut et délais de sécurité. Mais la seule réduction des facteurs augmentera le risque de pénurie. La vraie solution consiste à identifier les sources de variabilité et de risque, à les réduire, puis à abaisser les facteurs de compensation en conséquence.
Chaque facteur de compensation tient compte d'un type particulier de variabilité ou de risque. Diminuez la variabilité et vous pouvez diminuer son facteur de compensation.
Prenons l'exemple du stock de sécurité. Le stock de sécurité est souvent utilisé - il est d’ailleurs le seul lorsque les utilisateurs ne comprennent pas toutes les options et à quoi elles servent. Néanmoins, le stock de sécurité compense la variabilité de la demande ainsi que la variation de l'offre - par exemple les retards de livraison d'un fournisseur, des enregistrements d'inventaire inexacts, la mise au rebut non déclarée, etc.
Le stock de sécurité est généralement établi en utilisant une règle empirique ou, au mieux, des règles et des politiques pour certains groupes d'articles, comme le rapport volume élevé / volume faible ou les matières premières par rapport aux pièces fabriquées. Ces regroupements représentent le niveau de risque à prendre en compte.
Il existe deux approches générales pour comprendre la relation qui existe entre le risque et la compensation : analytique et empirique. Dans la première approche, vous étudiez les performances passées afin d'identifier tout modèle ou toute tendance en matière de variabilité qui entraîne une demande plus élevée que prévu ou une offre moins élevée que prévue (et qui aurait entraîné une pénurie si le stock de sécurité n'était pas en place). À partir de ces informations, vous pouvez calculer la quantité appropriée de stock de sécurité pour un article ou un groupe d'articles afin de fournir un risque acceptable de rupture de stock.
Dans l'approche empirique, vous vérifiez les registres pour déterminer le nombre réel de pénuries qui se sont produites avec la quantité actuelle de stocks de sécurité. Ensuite, vous supprimez une quantité modeste de stock de sécurité et vous surveillez les pénuries. Si le nombre de pénuries n'a pas augmenté, vous pouvez gérer ce stock de sécurité à partir de ce moment. Vous voudrez peut-être répéter l'expérience pour déterminer la quantité minimale de stock de sécurité qui donne un niveau de service acceptable.
Les mêmes approches peuvent être appliquées aux autres facteurs de compensation :
- La freinte des stocks compense les pertes non liées à la production (perte, détérioration ou expiration dans le magasin, par exemple). Cela peut également être utilisé pour compenser les erreurs et les inexactitudes de l'inventaire, ainsi que le stock de sécurité. L'exactitude des inventaires est l'une des plus grandes sources de variabilité dans les entreprises. Elle peut être améliorée grâce au comptage cyclique et à une plus grande discipline dans la gestion et la déclaration des mouvements de stocks.
- Les facteurs de rendement et de rebut s'appliquent aux pertes de production. Si le processus se traduit généralement par des pertes, qu'il s'agisse de pertes de composants ou d'articles en fin de production, il existe des espaces dans votre système pour reconnaître et compenser les besoins en composants supplémentaires, de sorte que vous disposez de la quantité requise à la fin de la production. Un feedback rigoureux (rapports d'inventaire et rapports sur les activités en atelier) vous aidera à maintenir ces facteurs sur la bonne voie.
- Il n’existe pas de solution facile pour les changements de planning durant les périodes de fabrication, et aucun facteur de compensation spécifique autre que le stock de sécurité. Il est recommandé d'établir et de respecter une période fixe dans le schéma directeur et de communiquer clairement au personnel des ventes et au service clients que promettre des expéditions hors de cette zone détruit les profits.
D'autres réductions de stocks sont possibles lorsque les délais sont réduits. Des délais d'exécution plus courts occasionnent moins d’imprévus (variabilité) et, par conséquent, justifient une réduction des facteurs de compensation qui se traduiront par une diminution des stocks. Des délais d'exécution plus courts vous permettent également de conserver moins de stocks tout en assurant la disponibilité nécessaire.