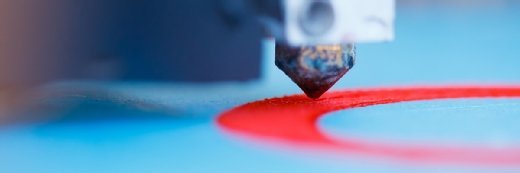
nikkytok - Fotolia
Ces principes de la fabrication additive qui s’appliquent à la conception de produits
La fabrication additive est l’une des principales technologies émergentes de l’industrie 4.0. Ce procédé porte en lui de nombreuses promesses. Mais son utilisation ne manque pas d’implications en amont, durant la phase de conception.
La transformation numérique de l’industrie promet de rendre plus connectée et plus agile la production, incitant les industriels à investir massivement pour ne pas rater le virage de cette 4e révolution.
Aujourd’hui la fabrication additive est l’une des principales technologies émergentes de l’industrie 4.0 en matière de personnalisation, d’innovation de produits ou de rapidité de fabrication. Son principe : réaliser une pièce directement à partir d’un modèle numérique 3D, par ajouts de matière. Ce mode de fabrication par addition de couches permet la fabrication rapide de pièces prototypes ainsi que la production de pièces intégrant davantage de fonctions que leurs homologues, produites par des procédés traditionnels.
Durant les premières années de la fabrication additive, ses applications concernaient essentiellement les phases amont de la conception de produits comme le prototypage. Ce n’est que depuis une dizaine d’années que l’on peut considérer une avancée suffisante des procédés de fabrication permettant ainsi une production en petite série de certaines pièces manufacturées.
Aujourd’hui les perspectives de croissance du marché de l’impression 3D sont prometteuses. Près de 76 % des entreprises françaises en ont fait le pari depuis 2020. Le marché mondial représente actuellement 15 milliards de dollars et les estimations prévoient un chiffre d’affaires de plus de 40 milliards de dollars en 2024.
La fabrication additive devient donc progressivement l’une des technologies clés du manufacturing avancé et est désormais au cœur de la transition numérique industrielle.
La conception au cœur du processus d’impression 3D
En fabrication additive, certains principes doivent être respectés afin de profiter pleinement de tous les avantages de cette technologie de pointe. Ces méthodes sont regroupées sous le terme de « Design for Additive Manufacturing » (DFAM).
La DFAM a ainsi pour ligne directrice plusieurs principes fondamentaux :
- Le choix de la technologie, du matériau ainsi que le procédé de fabrication associé. Cette combinaison doit être bien choisie dès la phase de conception afin de réduire le poids de la pièce, son nombre de composants, et augmenter ses propriétés mécaniques en vue de son utilisation,
- L’orientation de la pièce ou la direction de la conception. C’est-à-dire le placement de la pièce sur le plateau d’impression qui déterminera la qualité finale de la pièce,
- Enfin, une conception adaptée permettra d’anticiper les phases de post-traitement et d’essais afin d’en simplifier et minimiser les étapes.
Selon une étude de OnePoll pour Reichelt Elektronik, ayant interrogé des responsables d’entreprises de différents secteurs (industrie, logistique, pharmacie, énergie, etc.), l’ensemble de ces principes pris en considération pendant la phase de conception permettent aujourd’hui aux industriels « d’élargir la gamme de produits (59 %), d’augmenter la productivité (51 %) et de développer de nouveaux domaines d’activité (50 %). »
L’impression 3D apparaît donc comme un nouveau moyen de conception et production, servant de complément et de supplément aux techniques actuelles d’usinage classique. Elle offre ainsi une plus grande liberté de conception, une capacité à créer des produits finaux plus fonctionnels. Elle permet également de créer des pièces dans un délai de fabrication plus court, de limiter les déchets et d’en réduire les coûts.
Ainsi, pour répondre aux différentes utilisations de la fabrication additive en industrie, de nombreux procédés de fabrication sont exploités : FDM (Fused Deposition Modeling), SLA (Stereolithograph Apparatus), Binder Jetting, Polyjet, Stratoconception, SLS (Selective Laser Sintering) ou encore le DED – Directed Energy Deposition/CLAD – Constructive Laser Addictive Directe.
La technique la plus utilisée en industrie est celle de la SLS. Cette dernière se caractérise par son laser à forte puissance qui, par son énergie, provoque la fusion et la solidification d’un matériau sous forme de poudre. Ce procédé de fabrication convient ainsi parfaitement aux pièces à géométrie complexe, notamment lorsqu’elles présentent des détails internes, des parois minces ou des formes négatives.
Du maquettage et prototypage à l’impression 3D
Des applications courantes et bien connues de l’impression 3D sont le maquettage et le prototypage rapide. Ce sont des étapes primordiales lors de la conception d’un produit. Après structuration des besoins, recherche et élucidation de la solution, on s’assure de sa faisabilité.
L’impression 3D est l’un des procédés qui répondent le mieux à cette concrétisation rapide de la solution. Le produit se construit ensuite progressivement par itérations successives. À chaque itération, le prototype est évalué puis amélioré à partir des résultats des tests, jusqu’à validation du concept.
Le procédé de fabrication le plus utilisé pour le maquettage par impression 3D est le dépôt de fil fondu (FDM). Breveté en 1989, ce type de fabrication a pu être exploité en industrie seulement à partir de 2009 lorsque les brevets FDM ont expiré, ouvrant la voie à un fort développement de cette technologie. Ce procédé fonctionne grâce à un filament thermoplastique qui, chauffé et fondu dans une buse chauffante, additionne couche par couche le matériau.
Les pièces à développer sont alors modélisées, simulées numériquement et optimisées sur des systèmes de CAO (Conception Assistée par Ordinateur). Il en résulte que les fichiers numériques des pièces existent et peuvent donc être directement utilisés pour fabriquer ces pièces en impression 3D.
Le maquettage par impression 3D donne par la suite lieu à l’optimisation topologique des pièces, au moyen de nombreux tests sur la géométrie de la pièce dans des délais très courts. La solution consiste généralement à « supprimer » de la matière pour optimiser le design en fonction d’une ou plusieurs contraintes fonctionnelles (tenue mécanique, allègement…).
Le maquettage en impression 3D permet aussi de « dérisquer » des points particuliers comme par exemple la montabilité/démontabilité de la pièce, l’accessibilité des connecteurs, le positionnement/fixation du câblage…
L’association de la CAO et de l’impression 3D permet ainsi l’anticipation des erreurs et l’amélioration rapide de la qualité de conception augmentant alors la productivité du concepteur.
De plus en plus d’industriels séduits par la fabrication additive
Prenons pour exemples différents industriels qui ont investi ces dernières années dans la fabrication additive. Grâce à ce nouveau procédé, ces derniers y trouvent le moyen de faire passer leur production à un niveau supérieur.
Prenons l’exemple du constructeur automobile américain General Motors (GM). Son objectif : devenir « une entreprise plus agile et innovante » grâce à l’ouverture d’un centre dédié à l’impression 3D, a expliqué Audley Brown, directeur de la conception additive et de l’ingénierie des matériaux au sein de GM. Les conduits imprimés utilisés pour le développement de la Chevrolet Corvette en 3D ont permis par exemple d’économiser d’après le groupe « neuf semaines de développement et de réduire les coûts de conception et de fabrication de plus de 60 % ».
Le géant américain a déjà par ailleurs expérimenté le design génératif : processus de conception itératif qui génère de multiples résultats de conception répondant à des contraintes prédéfinies. Cette nouveauté est possible grâce à l’arrivée de nouveaux logiciels sur le marché, permettant d’analyser et de concevoir de façon automatisée une pièce. Couplés à la fabrication additive, ils permettent notamment la réduction de masse des pièces ainsi que leur consolidation : c’est-à-dire la création d’une nouvelle pièce composée de plusieurs composants différents et réunis en une seule pièce imprimée en 3D. Le groupe y voit d’incroyables opportunités.
On retrouve aussi L’Oréal, référence dans l’industrie cosmétique, qui investit depuis presque 30 ans dans la fabrication additive et de façon marquée depuis 2018. Le groupe possède aujourd’hui une soixantaine d’imprimantes 3D. Pour Matthew Forrester, responsable du déploiement de la fabrication additive au sein du groupe, cette technologie permet d’apporter de l’agilité de la conception à la fabrication : « nous pouvons à présent designer un produit et tester son ergonomie dans la journée ». Ce qui permet aux concepteurs de sélectionner plus rapidement les bonnes hypothèses de conception techniques.
Le groupe Renault, quant à lui, très investi depuis plusieurs années dans la numérisation de l’industrie, transforme petit à petit son usine de Flins, située dans les Yvelines. Son objectif : trouver une nouvelle manière de concevoir et d’utiliser les véhicules en prolongeant leur durée de vie. Le constructeur français ouvre ainsi un service de fabrication additive pour repousser l’obsolescence de ses voitures et qui permettra d’imprimer, par exemple, des pièces devenues indisponibles. Ce centre dédié à l’impression de pièces détachées s’inscrit donc dans une démarche de production propre à l’industrie 4.0.
Les défis de la fabrication additive
Bien que la fabrication additive ouvre la voie à de nouveaux modèles de production plus agiles, cette dernière présente néanmoins des vulnérabilités notamment en matière de propriété intellectuelle et de contrefaçon. En effet, il peut arriver que les opérations d’impressions soient déléguées à un sous-traitant, nécessitant ainsi la mise en place de protections plus accrues. Les services IT devront alors s’assurer de la sécurité des fichiers de conception, et ce, de l’entreprise jusqu’au réseau du client en passant par le sous-traitant. Leurs objectifs : garantir l’authenticité des pièces et des fichiers d’impression, ainsi que la propriété intellectuelle.
Pour répondre à cet enjeu essentiel pour les industriels, certaines entités et certains organismes se sont alors penchés sur l’utilisation de la blockchain pour pallier cette problématique. Les blockchains permettent en effet un suivi décentralisé et redondant des informations sensibles, dont elles conservent une trace chiffrée et infalsifiable. C’est donc un moyen sécurisé de partage d’information entre parties prenantes, en garantissant un service de traçabilité afin de lutter contre les contrefaçons.
Grâce à la numérisation actuelle de l’industrie, de nouvelles possibilités émergent avec pour ambition de réduire le temps nécessaire pour atteindre les objectifs de performance souhaités, et donc les coûts associés. Elles poussent alors les industriels à innover. Aujourd’hui incontournable, l’intelligence artificielle permet de contribuer au procédé de fabrication lui-même et aux différentes caractérisations des pièces obtenues grâce à la fabrication additive. Son objectif : optimiser la fabrication de nouvelles pièces avec les performances souhaitées.
Ainsi, de plus en plus, les outils numériques font partie intégrante de la chaîne de valeur de la fabrication additive et jouent un rôle essentiel dans l’optimisation et la maîtrise des procédés de conception et fabrication. Industrie 4.0 et fabrication additive ont donc un avenir commun.