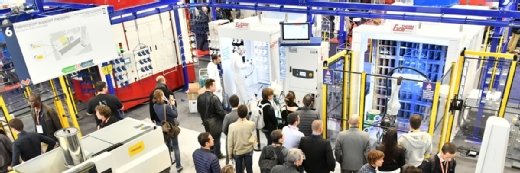
Smart Industries Lyon 2019 : l’usine connectée devient réalité
Ce salon européen confirme la mutation numérique de l’industrie qui s’appuie sur l’Iot, les logiciels de MES et l’analyse des données par l’IA. A la clé, une amélioration de la qualité des produits, une organisation du travail optimisée et une maintenance prédictive efficace.
Une usine connectée de 1100 m² bien réelle et fabricant des médailles personnalisées pour chaque visiteur du salon, a démontré concrètement toutes les possibilités de l’industrie 4.0.
Des robots, cobots (robots pilotés) et automates de transport et fabrication, gérés et pilotés par un centre de supervision, font connaitre la réalité de l’usine connectée. Les machines bardées de capteurs y renvoient les données pour le suivi de production, la qualité de fabrication et une analyse prédictive des défauts. Plusieurs briques technologiques permettent l’automatisation intelligente de la production.
Au cœur de l’usine intelligente, l’application de MES (Manufacturing Execution System) permet de gérer et optimiser toutes les étapes métier, depuis les ordres de fabrication en provenance de l’ERP ou du système de gestion, jusqu’au stockage et à l’expédition des produits. Le MES fournit aussi des indicateurs de traçabilité, de performance et de qualité comme le TRS (taux de rendement synthétique) un paramètre de suivi du taux d'utilisation de machines.
Les retours d’expérience des entreprises qui ont mis en œuvre un processus avancé de transformation numérique montrent que sa mise en œuvre est une évolution progressive et non une révolution technologique comme pourraient le faire penser les discours marketing.
« Avant de numériser les processus, il faut faire un état des lieux de l’existant » prévient Olivier Maho, responsable Industrie et logistique chez Somfy.
Une position partagée par Remi Chambard, Directeur Technique de l’unité d'Orléans-Saran John Deere, fabricant de moteurs industriels et agricoles. « Le projet s’est déroulé sur 3 ans. Nous avons eu une approche frugale, sans changer nos outils de production. Nous avons ajouté des capteurs sur les machines existantes et traité les données collectées. Par exemple, l’analyse détaillée du bruit des moteurs pour identifier les défauts sur les vilebrequins et paliers. Lors de l’usinage, nous détectons aussi la présence de copeaux via des capteurs. Nous avons obtenu une amélioration continue de la qualité des pièces, une meilleure prise de décision. Un laboratoire d’innovation partagée permettra à terme d’appuyer notre transformation numérique ».
La présence d’écrans permet le pilotage en temps réel de chaque unité et métier en affichant des informations précises sur la qualité et les incidents de production. La gestion des robots et cobots se fait via des tablettes. Côté IT, l’usine connectée, devra arbitrer la nature des données à confier au Edge Computing et au stockage en interne (nomenclatures, données projets, etc.) et au cloud externe. Tous les intervenants insistent pour affirmer que les technologies ne peuvent être imposées aux personnels sans leur acceptation ni pédagogie et sans le sponsoring actif de la direction.
Il faut gérer la cybersécurité et l’hétérogénéité des réseaux Iot
Emmanuel Couturier, Chef des programmes Innovation & Digital Aéronautique pour Safran Electronics & Defense explique : « Nous devons gérer les remontées des capteurs embarqués dans les avions, notamment sur les réacteurs et dans les ateliers. Le traitement des données se fait à proximité des équipements en mode edge computing. Nous identifions aussi les berceaux de support des moteurs qui se perdent dans les ateliers de nos clients. Mais la gestion efficace de nombreux flux de données hétérogènes issues des objets connectés reste un problème non résolu ».
En multipliant les points d’entrées, les objets connectés ouvrent des portes d’attaques sur le SI, ce qui implique, notamment, la gestion complexe des clés de cryptage des données. Il reste encore beaucoup de chemin à parcourir pour les industriels pour aller vers une transformation numérique complète. L’enquête de BPI France de 2018 indiquait que 70 % des chefs d’entreprise en faisaient un objectif prioritaire. Un optimisme tempéré par la réalité de cette transformation, puisque seules 37 % des industries ont avancé dans leur projet en ayant au moins franchi une première étape avec succès.
Des problèmes résolus chez EDF via le traitement intelligent des données
Une équipe de 20 personnes comprenant des data scientists et analystes sous la direction de Christophe Massis, Directeur Data Analytics Production, est chargée de traiter les problèmes de production d’électricité dans un délai de 6 mois. Dans le domaine nucléaire, il s’agissait d’un incident de condensation des circuits de vapeur. Après une présélection des données, l’équipe a isolé 40 paramètres traités en machine learning et identifié la cause. Cela évite les arrêts fortuits et améliore la maintenance, élément essentiel et très lourd dans le nucléaire.
Un gain de temps et d’argent. Dans les centrales hydrauliques, il fallait résoudre un problème de vibrations dans les turbines entrainant une surchauffe des paliers. « Le big data nous a permis une meilleure compréhension des phénomènes en identifiant des facteurs inattendus. Nous remplaçons désormais les paliers avant leur dégradation durant l’été, période de moindre production. C’est un gain de temps et d’argent, pour plusieurs millions d’euros car ces mesures sont déployées sur l’ensemble du parc de production d’électricité », précise Christophe Massis.
La cellule Data analytics a résolu avec succès la moitié des 20 cas d’usage adressés par les clients d’EDF.