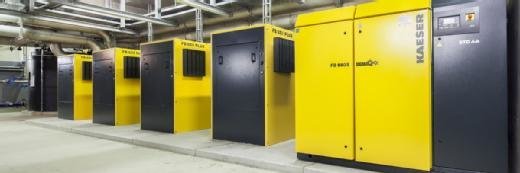
Kaeser met en place une maintenance prédictive de ses compresseurs sur SAP HANA
Le constructeur allemand de compresseurs s'est allié à SAP afin de connecter ses produits à son système d'information. Un pas décisif vers la mise en place d'une offre "as a service" qui intègre une maintenance prédictive s'appuyant sur HANA.
Kaeser Kompressoren est un industriel basé en Bavière dont la production va bien au-delà des compresseurs mobiles de chantiers. L'entreprise compte aujourd'hui 5 000 personnes et exporte tant dans l'Union Européenne qu'aux Etats-Unis et dans la zone Asie/Pacifique. On retrouve ses systèmes de compression d'air chez de nombreux industriels comme Air Liquide, Unilever, Yoplait ou Coca Cola.
C'est pour répondre aux attentes de ses grands clients que Kaeser est entré dans l'ère de l'Internet des objets en connectant ses systèmes de compression d'air à son système d'information. « Ce sont certains de nos clients qui nous ont demandé de fournir de l'air comprimé sous forme de service » souligne Falko Lameter, DSI de l'entreprise. « Ces industriels ne souhaitent pas avoir de personnel dédié à la maintenance de ces machines, ils préfèrent souscrire à un service »
Kaeser Kompressoren doit gérer ces équipements avec ses propres équipes de techniciens, ce qui est loin d'être simple pour une entreprise présente dans une cinquantaine de pays. Après avoir utilisé des solutions de prise de contrôle à distance pour réaliser des diagnostics à distance, Falko Lameter a décidé en 2011 de repenser le modèle de maintenance de l'entreprise.
Un projet mené en co-innovation avec SAP
C'est à cette époque que le DSI rencontre SAP qui cherchait alors un partenaire en co-innovation sur cette thématique de l'Internet des objets et de la maintenance prédictive. « Nous avons organisé avec SAP un workshop de type "Design Thinking" afin de mettre les idées en commun de gens venant du commercial, des services, de la R&D et des représentants de nos clients ».
De ce processus a émergé des idées, parfois loufoques. Les commerciaux voulaient un affichage têtes haute pour les guider jusqu'à leurs clients, la R&D voulait pouvoir tout analyser du fonctionnement des compresseurs, etc. En parallèle à ces réflexions, la DSI a commencé à collecter manuellement des données sur les compresseurs chez ses clients. A l'issue de leurs interventions, les techniciens ramenaient eux-mêmes les données et celle-ci étaient chargées dans la base de données HANA déployée en interne.
Ce projet de co-innovation est une conséquence d'une longue collaboration entre l'industriel et SAP. Il fut l'un des premiers à déployer R/3 en 1992, puis à faire évoluer son ERP pour en faire une plateforme globale, avec une seule instance SAP pour les 50 pays où est implantée l'entreprise. Aujourd'hui ce sont 4.500 personnes qui utilisent la Business Suite SAP. « Il y a trois ans, nous avons pris la décision de migrer vers HANA, une migration qui est aujourd'hui achevée » précise Falko Lameter.
Le CRM a été le premier à migrer vers la base de données In-memory de SAP afin de satisfaire les commerciaux qui souhaitaient un accès plus rapide aux données. Puis, c'est le volet Datawarehouse et Business Intelligence qui a migré vers HANA, puis la Supply Chain (SAP APO).
La station de compression devient une extension du SI de l'industriel
C'est en 2013 que le projet de mise en place d'une maintenance prédictive est initié.
Premier produit de l'industriel à être connecté en temps réel, le Sigma Air Manager 2. Il s'agit d'une station de compression d'air qui se compose typiquement de 3 compresseurs plus d'une station de traitement d'air.
Kaeser Kompressoren la commercialise depuis le début de l'année 2015. Chaque composant de la station est relié à l'ensemble via un réseau local IP et non plus un réseau industriel comme c'est généralement le cas pour ce type d'équipements. « Jusqu'à 2008, nous utilisions des contrôleurs Siemens pour nos stations mais maintenant nous concevons nos propres contrôleurs ainsi que l'ordinateur de gestion » explique le DSI.
Les SAM 2 s'appuient sur un Linux embarqué sur lequel les ingénieurs développent les logiciels en C++ et JavaScript. Le client IoT de SAP envoie les données en streaming depuis la station jusqu'au datacenter où les données sont stockées dans HANA. Chaque compresseur peut envoyer jusqu'à 200 paramètres différents chaque seconde (température, pression, notifications, etc.) à un PC industriel sur lequel un premier niveau de traitement des données est effectué. Puis le client IoT envoie à HANA ces données via une liaison VPN sur une ligne DSL dédiée.
Dès lors, ces données peuvent être analysées au siège par des experts via ce que l'industriel nomme la « Kaeser Plant Control Center », tour de contrôle qui surveille en mode 24/7 le fonctionnement des installations en production chez ses clients.
Outre le monitoring de l'activité, la génération de rapports, le suivi de consommation électrique ou encore l'établissement des plannings de maintenance, ces experts commencent à utiliser des algorithmes prédictifs afin d'anticiper les pannes potentielles.
L’information est aussi accessible aux techniciens amenés à intervenir sur les machines via un accès mobile, et aux équipes commerciales qui peuvent toujours consulter les évolutions d'activité de la station de compression avant de se rendre chez le client.
« Kaeser Kompressoren a cette vision de passer d'un modèle où ils construisent des compresseurs à un modèle fondé sur la vente d'un service » s'enthousiasme Steve Lucas, président de SAP Platform and Analytics.
Une plateforme HANA on-premise, pour l'instant
Kaeser Kompressoren met en œuvre une plateforme HANA hébergée en interne, sur ses propres serveurs. « Nous avons lancé notre projet trop tôt pour pouvoir le déployer sur la plateforme Cloud HANA de SAP » reconnait Falko Lameter qui ajoute : « comme il s'agit d'un co-développement, ce que nous avons développé n'est pas totalement standard avec l'offre Cloud HANA actuelle. Nous devrons réfléchir à comment nous allons ramener au standard SAP ce que nous avons développé. C'est en cours de réflexion sachant que cette solution sera disponible commercialement tant en mode on-premise, Cloud privé ou Cloud public ».
L'architecture exploitée par Kaeser Kompressoren se compose de la base HANA sur laquelle les algorithmes prédictifs sont exécutés. Une base SAP IQ (ex-Sybase IQ) assure un stockage des données de type "near line storage".
Le DSI a fait le choix de ne pas utiliser Hadoop pour stocker les données envoyées par les compresseurs. Il s'en explique. « Nous avons la possibilité d'utiliser Hadoop en tant qu'extension grâce à Vora. Néanmoins nous n'en avons pas véritablement besoin car nos données sont de bonne qualité car déjà traitées au niveau de la machine. Pour les industriels qui doivent stocker les données directement issues des capteurs, elles doivent tout d'abord les stocker sur Hadoop pour assurer leur nettoyage. Il faut savoir que 40% des données générées par les capteurs sont erronées, dupliquées, etc. Il faut donc commencer par les nettoyer avant d'espérer pouvoir les exploiter ».
Pour ses algorithmes prédictifs, les ingénieurs exploitent la bibliothèque de fonctions statistiques fournie par SAP avec HANA. En outre, le support du langage R leur donne accès à des milliers de fonctions disponibles. Enfin, ceux-ci mettent en œuvre les outils issus de l'acquisition de KXEN.
500 clients pourraient bénéficier immédiatement du service IoT
Pour l'instant, peu de machines sont connectée en temps réel. De ce fait, les volumes de données sont encore maîtrisables sur l'informatique interne de l'industriel. Néanmoins, Falko Lameter estime que migrer vers le Cloud sera nécessaire si l'ensemble des compresseurs commercialisés par la marque sont un jour connectés.
« Pour pouvoir le faire, il nous faudra une architecture totalement déployée sur le Cloud. C'est un point clé pour parvenir à cela. De plus il faut que toute l'organisation se mette au diapason, c'est encore plus compliqué. Cela change la façon dont les gens vont travailler, doivent penser leur activité et cela demande du temps ».
Technologiquement, le DSI estime qu'il pourrait connecter très rapidement les compresseurs de 500 de ses clients, mais « potentiellement, ce sont 10 000 clients qui pourraient être intéressés par cette approche si nous arrivons à leur proposer une technologie prédictive à bas prix. En revanche, on ne pourra pas activer un streaming de données permanent sur tous nos compresseurs, notamment ceux qui sont mobiles et utilisés sur les chantiers. Il nous faudra mettre en place des transferts de données non plus permanents mais quotidiens. Ce sont des scénarios auxquels nous devons penser, mais tout sera connecté un jour ou l'autre ! »